A meltblown make machine transforms raw materials into meltblown fabric through the following process:
Raw Material Preparation: The process begins with the preparation of the raw material, which is typically polypropylene (PP) pellets or chips. The raw material is fed into the machine’s hopper.
Extrusion: The raw material is melted in an extruder, which is a heated barrel with a screw mechanism. The extruder applies heat and pressure to melt the polypropylene, converting it into a viscous molten state.
Filament Formation: The molten polypropylene is forced through a specialized spinneret, which is a plate with numerous tiny holes or nozzles. These nozzles are arranged in a specific pattern and size to create fine filaments.
Fiber Stretching and Cooling: As the molten polypropylene is extruded through the spinneret, high-velocity hot air or other methods are used to stretch and elongate the filaments while also cooling them rapidly. This process is known as attenuating.
Randomized Fiber Collection: The stretched and cooled filaments are collected onto a moving conveyor belt or drum, forming a random layer of fibers. The airflow in the machine helps to disperse and randomize the fibers, creating a nonwoven web.
Bonding: The resulting nonwoven web of meltblown fibers is then passed through a bonding stage. The most common method of bonding in meltblown technology is thermal bonding. Heat is applied to the web, causing the filaments to partially re-melt and fuse together at their contact points, forming a coherent fabric structure.
Finishing: After bonding, the meltblown fabric may undergo additional processes such as calendaring or surface treatments to enhance its properties, meltblown make machine improve uniformity, or add specific functionalities like hydrophobic or antimicrobial properties.
Winding and Cutting: The finished meltblown fabric is wound onto rolls for transportation or further processing. It can be cut into various widths or lengths, depending on the specific application requirements.
The entire process is typically automated and controlled by computer systems to ensure precision and consistency in filament formation, stretching, bonding, and other parameters. The resulting meltblown fabric exhibits fine fibers, high filtration efficiency, and good barrier properties, making it suitable for various applications such as filtration media, medical masks, protective apparel, and more.
What are the typical specifications and capabilities of a meltblown make machine?
The specifications and capabilities of a meltblown make machine can vary depending on the specific model and manufacturer. However, here are some typical specifications and capabilities you might find:
Production Capacity: Meltblown make machines are available in different production capacities, ranging from a few hundred kilograms per day to several tons per day. The capacity is influenced by factors such as machine size, configuration, and the number of spinnerets.
Filament Diameter: Meltblown machines can produce meltblown fibers with varying filament diameters. Typical filament diameters range from 1 to 10 microns, although specific machines can be designed to produce fibers with narrower or broader diameter ranges.
Filament Density: The density of the meltblown fabric can be controlled by adjusting the machine’s parameters, such as the extrusion rate, stretching mechanism, and bonding conditions. The density affects the filtration efficiency, breathability, and other properties of the fabric.
Web Width: The width of the meltblown fabric produced by a machine can vary. Typical machines can produce fabric with widths ranging from a few centimeters to several meters. The web width is determined by the size and configuration of the machine, as well as the specific application requirements.
Speed and Control: Meltblown make machines operate at varying speeds, typically measured in meters per minute. The speed influences the production capacity and the quality of the resulting fabric. Modern machines often feature advanced control systems to precisely adjust parameters such as temperature, air velocity, and extrusion rate.
Material Compatibility: Meltblown machines are primarily designed for processing polypropylene (PP) as the raw material. However, some machines may have the capability to process other thermoplastic polymers as well, such as polyethylene (PE) or polylactic acid (PLA), depending on the specific machine design and configuration.
Energy Efficiency: Many modern meltblown make machines are designed with energy-efficient features to minimize power consumption. These features may include advanced heating and cooling systems, optimized airflow management, and intelligent control algorithms.
Automation and Integration: Meltblown make machines can be equipped with automation features and integrated with control systems for efficient and precise operation. Automated systems can monitor and adjust parameters, detect and respond to issues, and provide real-time production data for analysis and optimization.
It’s important to note that the specifications and capabilities of meltblown make machines can vary significantly based on the specific needs of the industry, production requirements, and technological advancements. Consulting with manufacturers or suppliers can provide more detailed and up-to-date information on the specifications and capabilities of specific meltblown make machine models.
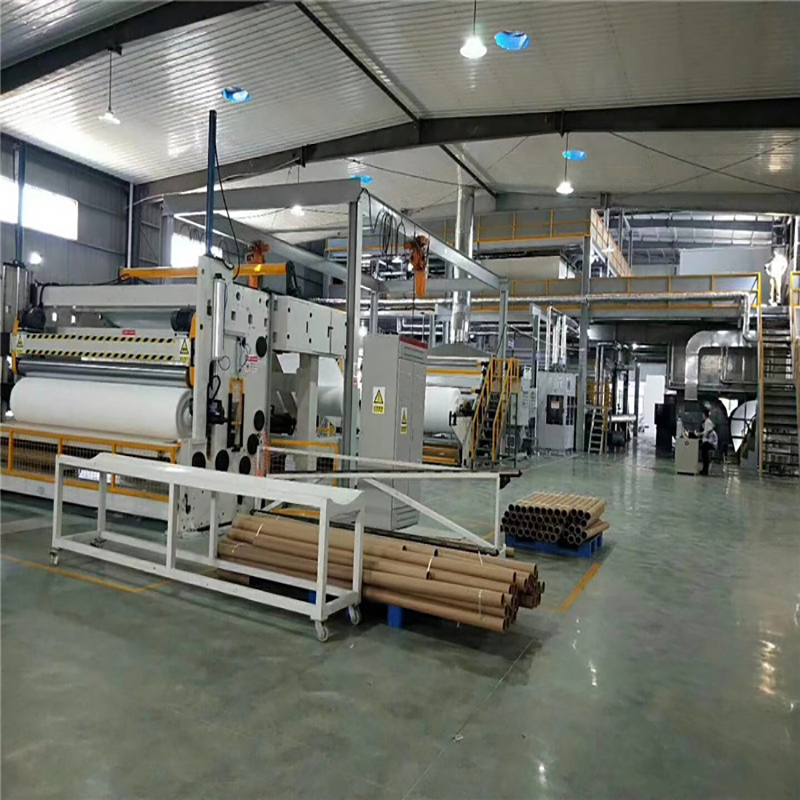